Case Study: Pollux PLM: An Analysis on streamlining technical errors and streamlining processes
Pollux PLM is a cutting-edge Product Lifecycle Management system designed to streamline product development processes and significantly reduce technical errors throughout the lifecycle of a product. This case study examines the implementation and impact of Pollux PLM within our organization, highlighting its role as a centralized platform that enhances collaboration, improves data accuracy, and accelerates time-to-market.
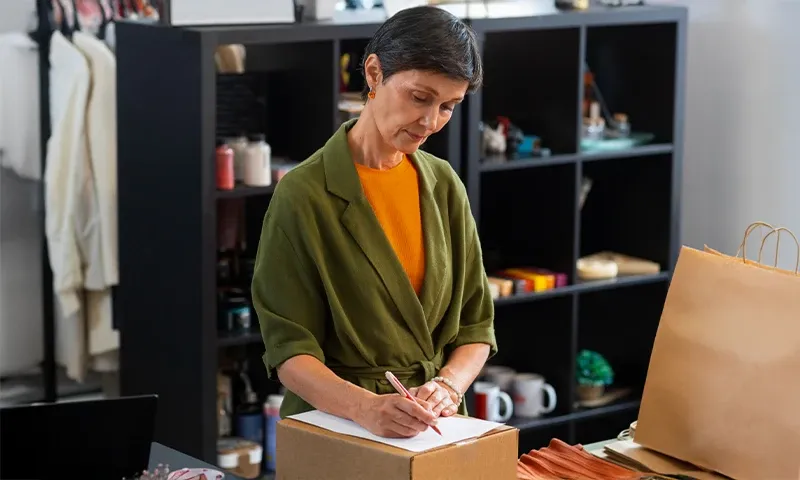
Pollux PLM is a cutting-edge Product Lifecycle Management system designed to streamline product development processes and significantly reduce technical errors throughout the lifecycle of a product. This case study examines the implementation and impact of Pollux PLM within our organization, highlighting its role as a centralized platform that enhances collaboration, improves data accuracy, and accelerates time-to-market.
By consolidating all product-related information—such as designs, specifications, and compliance documentation—into a single source of truth, Pollux PLM eliminates the inefficiencies associated with disparate tools and manual processes. The system’s integrated workflows facilitate real-time communication among cross-functional teams, allowing for rapid identification and resolution of potential issues before they escalate into costly errors.
The results of implementing Pollux PLM have been transformative. Our organization has experienced a marked decrease in development costs due to reduced rework and faster decision-making processes. Additionally, the enhanced visibility provided by Pollux PLM has led to improved product quality and increased customer satisfaction. Through this analysis, we aim to demonstrate how Pollux PLM not only mitigates technical errors but also streamlines processes to foster innovation and drive business success.
In today’s fast-paced market environment, companies face increasing pressure to deliver high-quality products quickly while minimizing costs. Technical errors during product development can lead to significant delays, increased expenses, and ultimately a loss of competitive advantage. Recognizing these challenges, our organization developed Pollux PLM—a robust Product Lifecycle Management system tailored to streamline product development processes and enhance overall operational efficiency.
Pollux PLM serves as an integrated platform that centralizes all aspects of product data management. By providing a comprehensive view of product information—from initial concept through design, manufacturing, and market launch—Pollux PLM empowers teams to collaborate effectively and make informed decisions based on accurate, up-to-date data. This case study explores the multifaceted benefits of Pollux PLM in reducing technical errors and optimizing workflows across various departments.
- Centralized Data Management
All product-related documents and specifications are stored in one location, reducing the risk of miscommunication and data loss.
- Real-Time Collaboration
Integrated communication tools allow teams to share updates instantly, fostering a culture of transparency and accountability.
- Automated Workflows
Streamlined processes minimize manual tasks, enabling teams to focus on innovation rather than administrative burdens.
Through this analysis, we will delve into specific examples of how Pollux PLM has transformed our product development lifecycle by mitigating technical errors and enhancing process efficiency. The insights gained from this case study will serve as a valuable resource for organizations seeking to implement or improve their own PLM systems in pursuit of operational excellence.
- Difficulty with rapid pace of Growth
- Technical issues
- Processing large volumes of data
- Lack of tools
- Low/No processes
- Accurate tech packs and grading
- Tech pack templates save time
- Established standard processes
- Fewer data errors
- Ability to work remotely
With over 40 components per dress, overseeing numerous raw material suppliers for each item of clothing was getting difficult. We had to ensure that everything was properly coordinated and there were no errors
- In order to manage the intricacy of each unique style, our client required a Product Lifecycle Management system (PLM) to set up formal procedures and standardize tech pack data. Additionally, they sought to increase communication and product development transparency.
- The ability of Pollux Software to demonstrate how inconsistent processes could be improved, the team's responsiveness, and the quick time-to-value of Pollux SMB, a cloud-based SaaS solution for small and medium-sized businesses, made us stand out.
- Pollux used a time efficient modular approach which meant ease of implementation and less involvement from the client team
- Operational excellence was ensured via Pollux, which became a single source of truth in a central data repository with well-defined procedures and nearly error-free tech packs.
As per the client - “The cherry on top was Pollux's extensive background in the fashion industry. It became clear that the Pollux team is well-versed in fashion. We could tell that they had experience working with other businesses that faced comparable seasonality problems and product development obstacles because they spoke the same language as our designers and production crew. We believed that our product category made sense for the solution, and Pollux's SMB is incredibly user-friendly. “
Our customer now boasts precise tech packing, PLM data management, and grading. With a category like women's clothing, and even more so with our client's special materials and design style, the crucial element is the high degree of accuracy needed as new fashions are introduced in a variety of sizes.
The PLM was used to digitally construct essential workflows. With all product data in one easily accessible digital location, email and spreadsheet product development are becoming obsolete, leaving no doubt about the most recent versions of anything.